As we know ethanol and water forms azeotropes and it is not possible to produce anhydrous alcohol by simple distillation process. So, due to this azeotrope formation we can purify ethanol up to 89 mole% only. Therefore, to get anhydrous alcohol we require different techniques like hydrophilic molecular sieves or azeotropic distillation. In this article we will go through the process simulation results of anhydrous alcohol plant using azeotropic distillation method. Also, here I have considered benzene as an entrainer to break the azeotrope. I have done this simulation using Chemcad Process Simulator.
Table of Contents
Anhydrous Alcohol Use
As we know crude is a limiting resource of energy and the fuel price is rising continuously. Therefore, to control these prices and for longer time sustenance we can use anhydrous alcohol and petrol mixture as a fuel to drive our vehicles. This blend of anhydrous alcohol and petrol we know as power alcohol. Power alcohol contains anhydrous alcohol or absolute alcohol between 5% to 25%, by volume.
Other than this, we can see anhydrous alcohol is widely used in industry. In industry we use it in synthetic organic reactions and as a solvent. This is because of its low toxicity and ability to dissolve non-polar substances. Moreover, medically we can use as a solvent and can inject into nerves and ganglia for relief of pain. Anhydrous ethanol is used as an antiseptic also. So, let us fix the basis for anhydrous alcohol plant process simulation first.
Basis for Process Simulation
So, to start process simulation let us consider below parameters,
Column Feed : 1000 kg/h
Composition of Feed : Ethanol – 89 mole%, H2O – 11 mole%
Feed Temperature : 45 0C
Anhydrous Alcohol Purity : 99.99 mole%
Entrainer : Benzene
Process Description of Anhydrous Alcohol Plant
In ethanol dehydration there are three columns which we can see in below figure. First column is Dehydration Column, second is Benzene Recovery Column and third is Water Removal Column. Therefore, we can divide whole process in three main steps as below.
Ethanol Dehydration
In Dehydration Column, we feed the azeotropic mixture of ethanol and water, which contain 89% ethanol and 11% water on mole basis. Also, we know this feed mixture as RS or Rectified Sprit, which is the final product of a distillery.
So, from dehydration column top ternary azeotrope of benzene with water and alcohol goes to condenser. The boiling point of this azeotrope is 65.8 0C. Subsequently, this ternary mixture after condensation forms two layers.
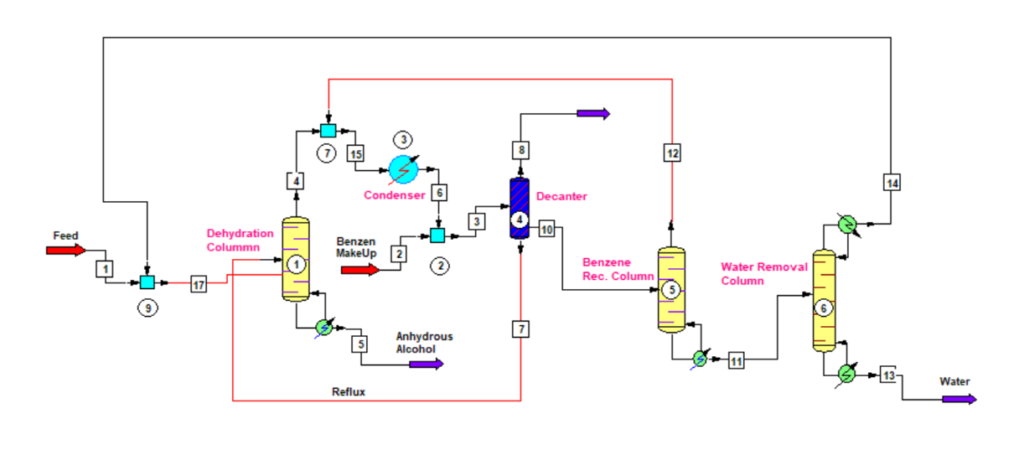
The vapor from benzene recovery column also mix with the vapor of dehydration column. This combined vapor after condensation goes to a decanter. From decanter water rich layer contains small amount of benzene goes to benzene recovery column. While, benzene rich layer is a reflux stream for the anhydrous alcohol column.
The bottom stream of ethanol dehydration column is 99.99 mole% ethanol, which we call anhydrous or absolute alcohol.
Benzene and Ethanol Recovery
From decanter water rich layer stream goes into the benzene recovery column. This column is just like a stripper, which strip out all the benzene from incoming feed. The bottom product of this column is free from benzene and this way we recover and recycle benzene to reduce the benzene consumption norm. In result reducing anhydrous alcohol manufacturing cost also.
The vapor outlet from benzene recovery column goes into the anhydrous column condenser. This stream contains benzene, ethanol and water. While, the bottom stream of this column is free from benzene and contains ethanol and water only. Hereafter, the benzene recovery column bottom stream goes into the water removal column or ethanol recovery column.
The purpose of water removal column is to recover ethanol from the incoming feed stream. Bottom stream of this column is as good as pure water and may contain traces of ethanol. So, this we can recycle inside the plant after suitable treatment. While the top stream is azeotropic mixture of ethanol, which we recycle back into the dehydration column feed tank.
Material Balance for Simulation
I conducted process simulation for ethanol dehydration plant using benzene as an entrainer. Below is the material balance table. And for stream name reference you need to follow above PFD. I have selected UNIFAC thermodynamic package for this system. Feed rate for the column is 1000 kg/h at 45 0C, containing 89 mole% ethanol and 11 mole% water. Moreover, column is operating at atmospheric pressure.
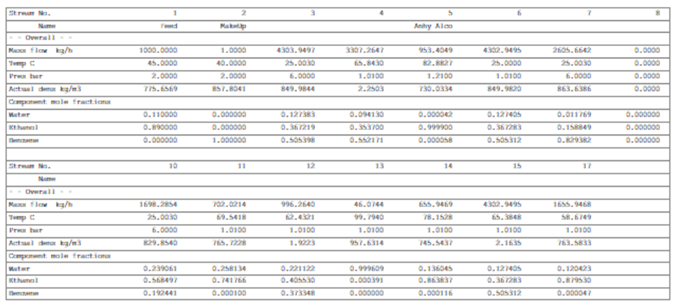
Below are the ternary azeotrope data which we can see in above table. We can see Stream-4 which is the vapor outlet of ethanol dehydration column and various details from simulation result are as follows.
Flow Rate : 3307.3 kg/h
Temperature : 65.8 0C
Composition : Water – 9.41 mole%, Ethanol – 35.37 mole%, Benzene – 55.22 mole%
Dehydration column vapor stream is combined with benzene column top vapor, Stream – 12 having below details.
Flow Rate : 996.3 kg/h
Temperature : 62.4 0C
Composition : Water – 22.11 mole%, Ethanol – 40.55 mole%, Benzene – 37.34 mole%
After condensation above two streams goes into a decanter vessel for layer separation. Moreover, to compensate any benzene losses (i.e., vent loss mostly), we do benzene make up on requirement basis. Material balance around decanter is summarized in below table.

Above data is important for the process design and process control of decanter.
Simulation Results for Distillation Columns
Below is the simulation output for all three distillation columns for your reference. Here you can see the reboiler duty, condenser duty, reflux rate, theoretical stages considered, etc.
Dehydration Column and Condenser Results
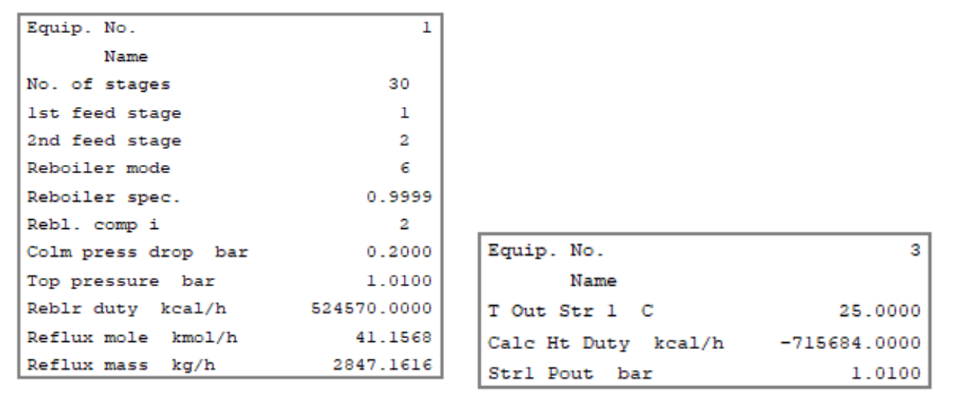
Benzene Recovery & Ethanol Recovery Column Results
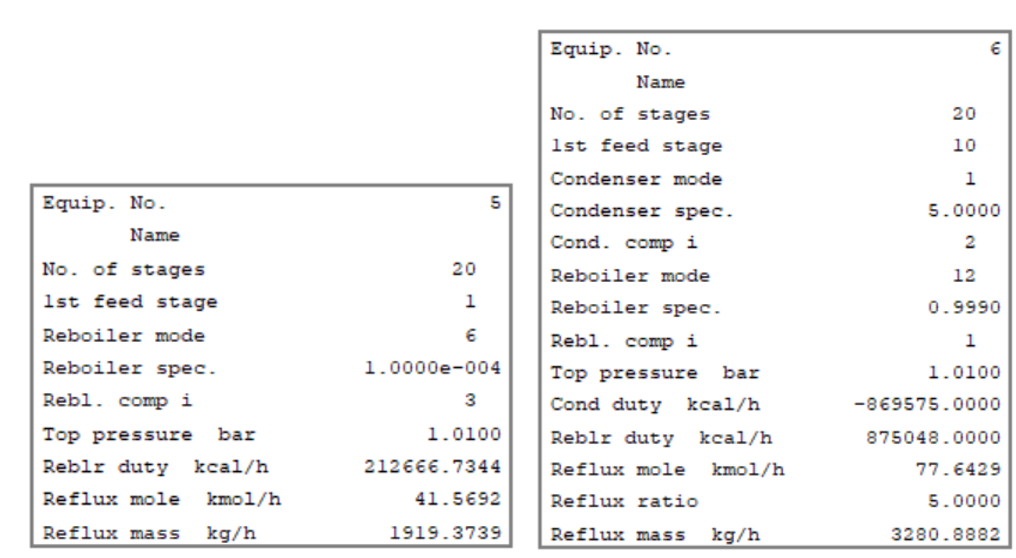
Conclusion
In my experience I have found these simulation results are in very good agreement with the actual plant data. So, we can see process simulators make our engineering efforts very fast and efficient. However, you should understand the process of that particular plant and behavior of components involved clearly. Because in a simulator if you put garbage in you will get bigger garbage out.
So, above results of process simulation of anhydrous alcohol plant gives you process insight. And, these data can be used further for optimization and process improvement objectives. From data comparison between simulation result and actual plant operation, we can find gaps in existing plant operation. So, after gap identification we can do brain storming with cross functional team to eliminate this gap. Afterwards, suitable improvement initiatives implementation will make our process more cost effective and safe also.
Thanks for reading and looking forwarding for feedbacks.