In Chemical Process Industries (CPI) we face the distillation problem of azeotropes or close boiling chemical mixtures. So, to break the azeotropes we can use several techniques like, azeotropic distillation using entrainers, extractive distillation using solvents, molecular sieves, and pressure sensitive distillation or PSD. However, we can find the use of first three methods in our CPI easily. But, use of pressure sensitive distillation is not so common. Moreover, sometimes PSD is also called pressure swing distillation method.
So, in this article we will focus on pressure sensitive distillation technique and will try to understand the concept behind. Moreover, we will take example for separating THF-Water azeotrope using PSD. For this we will develop a process flow diagram and also go through the material balance. For material and energy balance we will use CHEMCAD simulation results. So, first let’s understand the basic concept behind PSD.
Table of Contents
Concept Behind Pressure Sensitive Distillation
We can find, the composition of many azeotropes varies with system pressure. So, in such cases we can exploit this change in compositions of a binary azeotrope with pressure. To understand the concept let us assume we have a binary azeotrope having chemicals ‘A’ and ‘B’. And, say at 1.0 atm. pressure, the azeotropic composition is 30 mol% A and 70 mol% B. While, at 6.0 atm., the azeotropic composition may be 40 mol% A and 60 mol% B.Thus, we may be able to use the pressure sensitivity of the azeotrope to beak it. For, this purpose we will be using two distillation columns, operating at two different suitable pressures to produce pure A and B. To understand this, we can refer below figure.
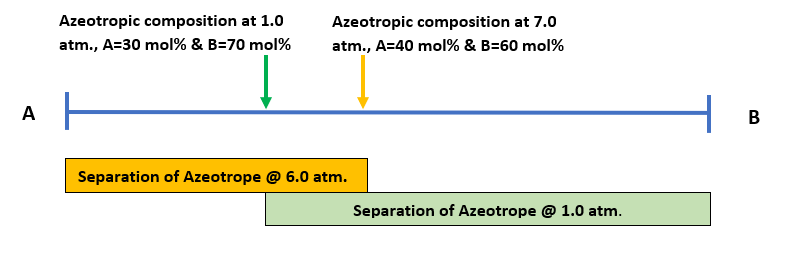
In our CPI, we can find some commercially viable applications of PSD includes, the separation of THF-Water, methanol-acetone, methanol-methyl ethyl ketone (MEK), acetonitrile-water, etc. The major problem faced in PSD system design is non-availability of mixture azeotropic data at different pressures. Most of the azeotropic data are available at atmospheric pressure only. And, data generation at non-atmospheric pressure will be very expensive. Therefore, this is the main reason, why process design engineer doesn’t choose to check the feasibility of PSD. While, this may be the best possible azeotrope breaking method.
Process Flow Diagram of PSD for THF-Water
So, let us discuss the separation process for THF-Water mixture using pressure swing distillation. Below figure shows, a two-column process to separate THF-Water binary minimum-boiling azeotrope. Here, the azeotropic composition at pressure 1.0 atm. is richer in THF component than the azeotropic composition at pressure 7.0 atm. The first column is operating at pressure 1.0 atm. and in this column, feed is a mixture of fresh feed and recycle stream from the second column. This mixed feed is such that the overall composition lies on the ‘Water’ side of the azeotropic composition at 1.0 atm. Pure water is recovered as bottom from column-1 and a mixture near the azeotropic composition is produced as distillate.
From here we pump this distillate stream at 7.0 atm. and fed to the second column. So, this column-2 feed is on the first component side (i.e., THF) of the azeotropic composition at 7.0 atm. From this column, pure THF is recovered as the bottom product. While, the azeotropic top composition is recycled to the first column.
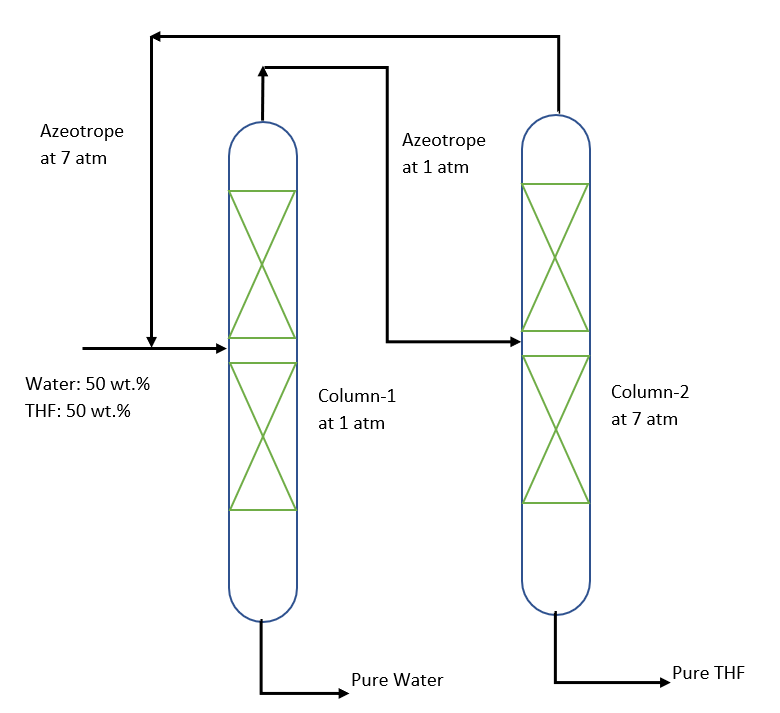
Equilibrium Diagram for THF-Water System
Below is the x y diagram for the THF-Water system at pressure 1.0 and 7.0 atm. for your reference. Here, we can see the azeotrope composition changes with the change in column pressure. At, pressure 1.0 atm. composition of THF: 82.56 mole% while, at 7.0 atm. composition of THF: 65.14 mole%. Which is a significant change in azeotrope composition with a reasonable pressure difference of 6.0 atm.
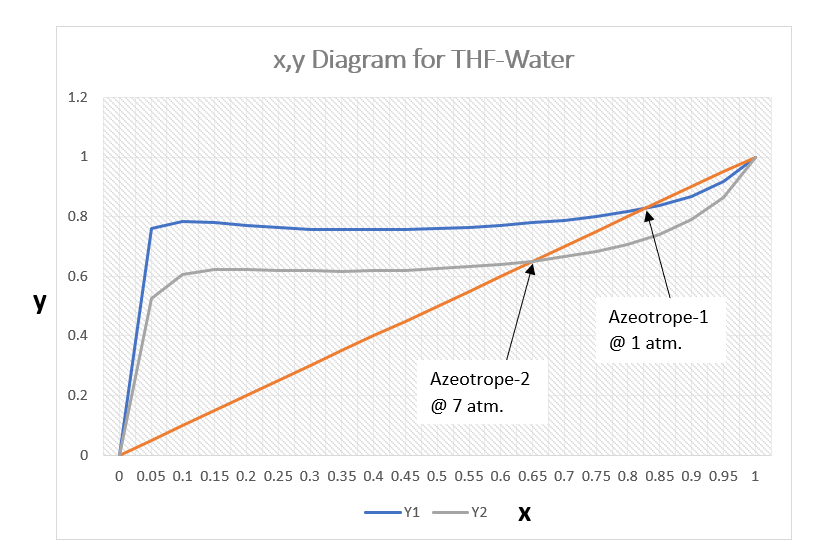
Material Balance of PSD for THF-Water
In this section we will go through the material balance table based on process simulation. In this process there are two columns, Column-1 operates at 1.0 atm. while, Column-2 operates at 7.0 atm. Fresh feed containing THF (Tetrahydrofuran) and water, mixed with the Column-2 distillate and enters into the Column-1. From the bottom of Column-1 we get pure water and distillate which is an azeotrope at 1.0 atm. pressure, goes into Column-2 via pump. The composition of Azeotrope-1 is THF: 82.56 mole% and Water: 17.44 mole%.
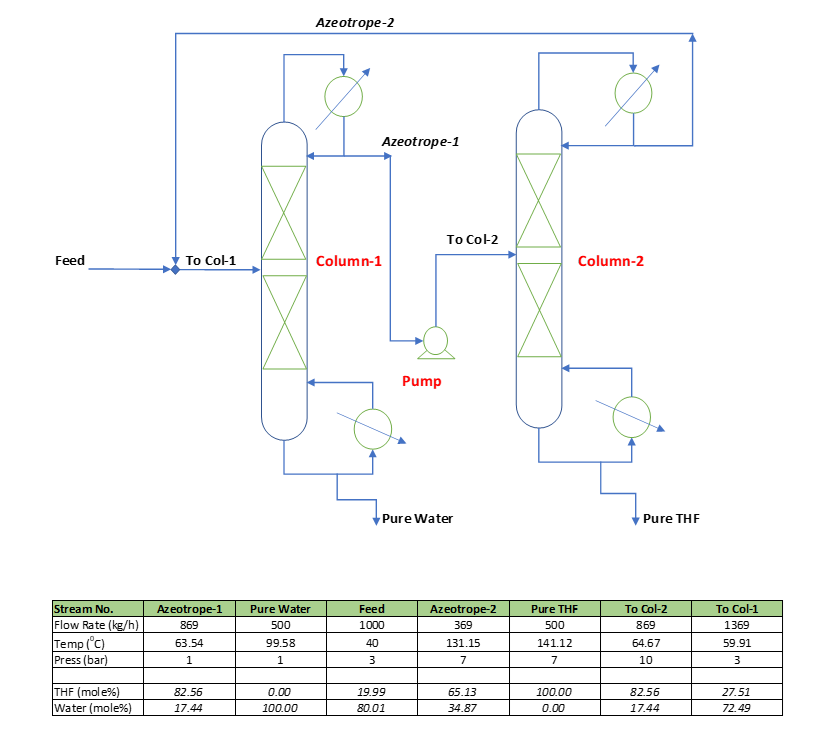
Column-2 is operating at 7.0 atm. pressure, and the Azeotrope-2 contains THF: 65.13 mole% and water: 34.87 mole%. From the bottom of this column, we get pure THF (Tetrahydrofuran). For detailed material balance we can refer to the above material balance table.
Pressure swing distillation has various limitations and difficulties as discussed in subsequent section.
Limitation of Pressure Sensitive Distillation
So, for the pressure-swing distillation feasibility, it is important that the azeotropic composition must vary significantly with column pressure. Moreover, pressure difference between two columns should not be more than 10 atm. Therefore, the change in azeotropic composition should be at least 5%, if it is 10% or more over this pressure range. Then, this azeotrope will be more feasible for PSD method.
Because, with a very large pressure range, we may need refrigeration for condensation of the low-pressure distillate. On other side at high pressure, column bottom temperature will be high. And this will result in high temperature utility requirement in reboiler.
In the case of smaller variation of azeotrope composition over the pressure range, there will be larger recycle streams between the two columns. In particular, for minimum-boiling azeotropes, the pressure-swing distillation approach requires high energy usage. Moreover, because of high flow rates large diameter columns are required, which leads to high capital costs for the setup.
Conclusion
So, in this article we discussed the pressure sensitive distillation or sometimes called pressure sensitive distillation. This technique we can use to break the pressure sensitive azeotropes. The major advantage of PSD method over azeotropic and extractive distillation is the avoidance of the use of entrainers and solvents. We understood the concept behind PDS and designed a pressure sensitive distillation system to break the THF-Water azeotrope. You can use this article to develop PSD system to break other azeotropes, which are pressure sensitive.
However, in this article we focused on minimum boiling homogeneous azeotrope. Similarly, you can develop for maximum boiling azeotrope also. In that case we will recover pure product as distillates from both the columns. While, bottom of second column will be recycled and mixed with the feed of first column.
I think this article should be helpful for you, thank for reading and looking for your valuable feedbacks.