This article is about understanding the process of a molten salt heating system. Before this let us discuss different types of heating systems, which we use in our chemical industries.
In our chemical plants, we need to heat exchange at various temperature levels. These temperature levels can be low, in the range of 50 – 130 0C, very high from 250 – 750 0C or even higher. Various heating requirements are like heat supply through reboiler in a distillation column, heat exchange in a fixed bed reactor to maintain the reaction temperature, thermal cracking of acetic acid in furnace coil, etc.
We can divide these heat supply sources in two categories, first is indirect heating system and second direct heating system. Let us discuss each of them as below.
Table of Contents
Indirect Heating Systems
When we talk about indirect heating systems, it means heat is supplied to a heat transfer media. And, this heat transfer media supply this to the process, using a heat exchanger, jacket or a coil. This heat transfer media can be water, thermic fluid (organic oils) or molten salt. And, different types of fuels, which we use for energy generation are coal, furnace oil, natural gas, etc. We can identify various types of main indirect heating systems in our process industries are as detailed below.
Boilers
Boilers are widely used in almost all process industries as a source of heating supply. In boiler we use water as a heat transfer media and main fuels are coal, natural gas & furnace oil. Boiler can generate steam at various pressures, which we use to supply heat to reboilers, evaporators, heaters etc.
In case of steam, as heating temperature increases required operating pressure of the boiler and process equipment goes up. For example, if we want to supply heat at 150 0C to a distillation column through reboiler. The require steam pressure is around 16 bar (as we need steam temperature between 190 – 200 0C).
Therefore, for higher process temperature requirements, say 230 0C we need much higher pressure (i.e., around 50 bar pressure saturated steam). For this pressure, we require higher thickness of shell, tube-sheet, flanges, tubes, nozzles, piping, etc. This will increase equipment cost and moreover possibility of hazardous will be too high.
So, for the heating requirement above 170 0C, using steam become uneconomical. The better substitute in this situation is thermic fluid heater.
Thermic Fluid Heater
As we discussed above for higher temperature heating requirements, thermic fluid is a better economical and safer option. For example, @230 0C temperature, required saturated steam pressure is 50 bar, which is very high. So, for heating requirements between 170 – 380 0C, we generally use thermic fluid heaters.
In thermic fluid heater we used different types of thermic fluids as a heat transfer media. These thermic fluids are either eutectic mixtures of high boiling organic oils or can pure single organic oils also. Based on the operating temperature requirement, we decide the type of thermic fluid. For heat supply to the thermic fluid, we use furnace oil, natural gas, electric heating elements or coal as a fuel.
For higher operating temperature around > 390 0C, thermic fluid starts degrading. Therefore, we need to replace the costly thermic fluid frequently into the system, to maintain its properties. So, it become a costly option at this high operating temperature for the process operation.
Molten Salt Heating System
For the temperature services higher than 380 0C, we can use molten salt heating system. As we discussed above, thermic fluid degrades rapidly at high operating temperatures. And, we need regular replacement to maintain its properties. Therefore, heating with thermic fluid becomes uneconomical.
In this case we can use nitrate based molten salt heater for heating requirements, which is thermally stable up to 500 0C and has melting point around 140 0C. One of the most commonly used molten salts is a eutectic mixture of sodium nitrate and potassium nitrate.
You need to provide proper heat tracing to avoid molten salt solidification problem. We will discuss this option subsequently in detail.
Direct Heating Systems
The example for this type of heating system is a Furnace or Fired Heater. Here, we fire the fuel in a burner fixed inside the furnace body. The heat is generated form fuel firing, which comprises radiative and convective heat components.
This heat is directly absorbed by the process fluid flowing through tubes. There is no heat transfer media as we had in indirect heating systems. These tubes or coils are located inside the furnace body.
In direct fired heater we can supply heat up to the highest possible temperature levels. The limitation is the melting point temperature of the tube material.
In direct fired heater possibilities of process hazardous are very high. As, in case of any leakage in tubes, process will come in contact with the direct flame. This will lead to plant fire and explosion also. Moreover, precise temperature control is also a big challenge in comparison with other indirect heating system options.
So, now we will discuss about molten salt heating system in more detail, among all the options as we have discussed above.
What is a Molten Salt?
From the name itself, it is evident molten salt is the state of a salt in a molten condition. At STP these salts are solid and forms an ionic solution in water. As we increase the temperature water evaporates and this salt converts into liquid phase known as molten salts.
We use molten salt because it is a liquid at atmospheric pressure, non-flammable, low cost and efficient for energy storage. For industrial heating requirements, the molten salt components are always used based on nitrate. In our plants generally, molten salts are eutectic mixture consisting of potassium nitrate, sodium nitrite and sodium nitrate, having a melting point of 142 °C. Under operational conditions they are liquid and are operated unpressurized.
The performance of molten salt is much higher compared than other organic oil. It can handle temperatures up to 500 0C, without thermal decomposition.
Molten salts remain in liquid phase at temperatures (500°C or higher) with little or no vapor pressure. Molten salts can replace organic or synthetic oils in heat transfer applications. In case of molten salt heat transfer media, we can operate our system at atmospheric pressure. Apart from this molten salt has low viscosity and high heat capacity.
While molten salts have substantial benefit with their high operating temperatures, simultaneously, they pose a challenge of very high freezing points (ranging from 120°C to 220°C).
Melting Points of Salt Systems
As we have discussed above, despite of having many advantages over organic oil, molten salts have very high melting points. This causes chocking inside the system, which is impossible to clean up. In most of the cases we need to cut the equipment for de-chocking. And, sometimes we scrap the equipment, which is a very costly situation for the business.
Therefore, we always try to go for a molten salt which has low melting point and remain stable at required working temperature. Below is the list of various nitrate salt system for your reference (Peng, et al., 2010).
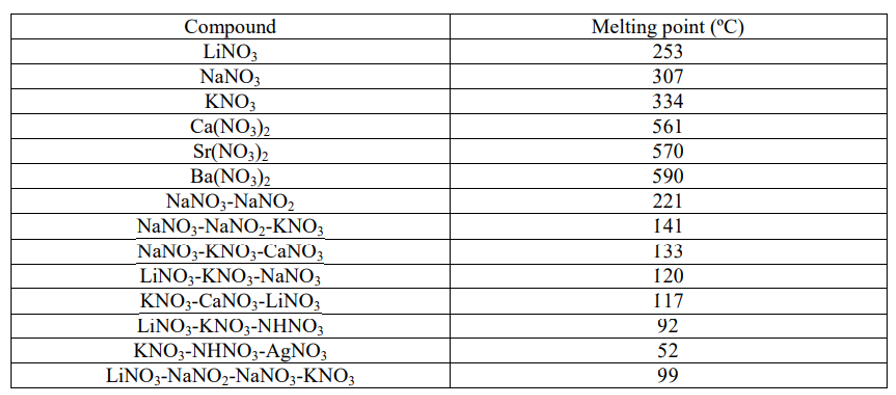
Phase Diagram for NaNO3 – NaNO2 Mixture
Below is the phase diagram of NaNO3 and NaNO2 mixture for your reference. Around at 40 mol% NaNO3 and 60 mol% NaNO2 it forms a eutectic mixture, which has melting point around 221 0C. This eutectic mixture will remain in liquid phase above this temperature. In other words, we can say this mixture has lower melting point in comparison with individual pure forms. Which is 307 0C for NaNO3 and around 271 0C for NaNO2.
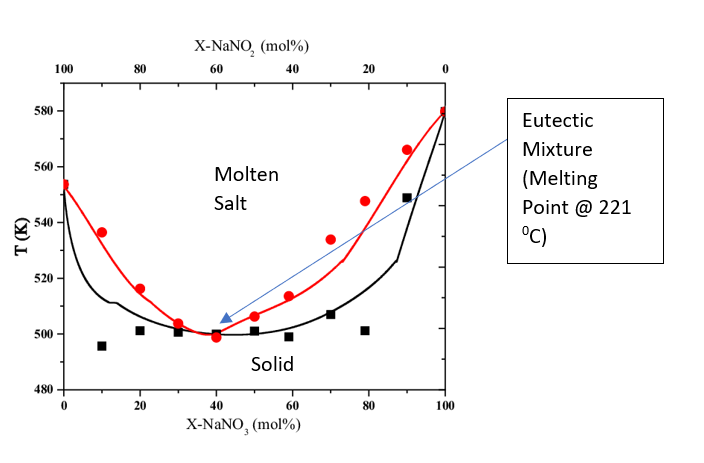
Process Flow Diagram for Molten Salt Heater for Fixed Bed Reactor
Gas phase chlorination of methyl-pyridine requires very high operating temperature. For example, 2-Chloro-5-Trichloromethyl Pyridine is produced by reacting β-picoline with chlorine in a gaseous phase at 300° to 500° C. Reaction happens, in the presence of an inert diluent of nitrogen, a halogenated methane, a halogenated ethane a halogenated ethylene or a mixture there of. The 2-Chloro-5-trichloromethyl pyridine is useful as an intermediate for medicines, agricultural chemicals, dyes especially herbicides.
For this process we can use a multitubular fixed bed reactor filled with silica pellets. Reactant gases go into the tubes and to maintain reactor temperature molten salt circulates in the shell side.
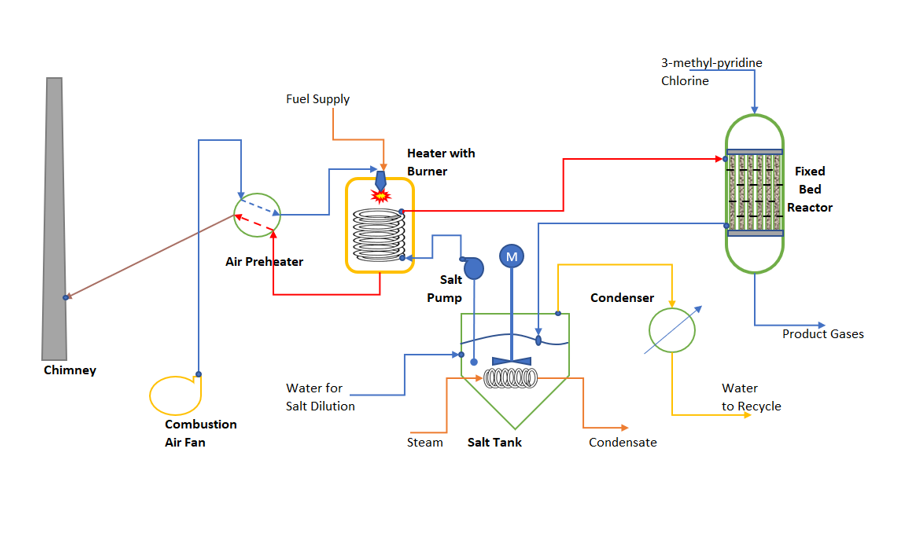
Various Parts of a Molten Salt Heater
In above PFD we can see there are various components of a molten salt heater as mentioned below:
Heater with Burner
Here we supply the heat to circulating molten salt by fuel firing or electrical heating elements. In fuel firing, fuel (i.e., natural gas or furnace oil) and combustion air enters into the burner. Firing takes place and heat is absorbed by circulation molten salt inside the furnace coils. Fuel firing rate is controlled as per the temperature requirement of the reactor.
Salt Tank
This tank is fitted with a heating system to maintain the melting point temperature of the salt. Moreover, there is an agitator which keep the mixture in homogeneous condition. There is a water supply line which we use in the start up of the system, to make the water-soluble salt solution. As, system temperature increase water evaporates from the system and goes to a condenser. In this condenser water is condensed and recycled back to the salt dilution. This salt dilution with water we do during start up and shutting down of the molten salt heater.
Molten Salt Circulation Pump
This pump should be suitable for high temperature conditions (i.e., around for 550 0C working temperature). Moreover, this pump should be jacketed, to avoid any chocking in case of low operating temperature conditions.
Combustion Air Pre-Heater
This is a very important equipment for the overall thermal efficiency of molten salt heater. Combustion air is preheated using outgoing hot flue gases before venting through the stack.
Fixed Bed Reactor
In above PFD molten salt is circulating inside the reactor shell. Here heat exchange takes place between tube side process fluid and shell side molten salt. The piping and reactor shell must be designed in such a way, that it can self-drain. This we need to make our reactor safe from any chocking because of any remaining residual material during shutdown. This is a most costly equipment of our process and we don’t want to damage it.
Condenser
To condense the water vapor coming out from Salt Tank we need this condenser. However, we can operate the system without this equipment also. But, for the environmental conservation reasons it is better to condense the water vapor and recycle back into the process. In condenser cooling water is used a cooling utility.
Conclusion
So, I think you got a good idea about a molten salt heater. Like, what is a molten salt? How a molten salt heater works? What are the challenges during operation?
For design calculation for a process heater, you need to follow below steps.
Calculate the heat requirement for your reactor.
Estimate the size of furnace considering efficiency around 75%. And estimate the fuel firing rate and combustion air requirement.
Estimate the molten salt circulation rate for the required heat load. Keep inlet outlet temperature difference of molten salt less than 10 0C. Also, molten salt supply temperature should be close to the reactor temperature (i.e., around 4-5 0C). This will help you to maintain the reactor temperature more precisely.
Thanks for your reading, looking forward for your feedbacks and comments.